Precision Plastic Injection Molding: Revolutionizing Manufacturing
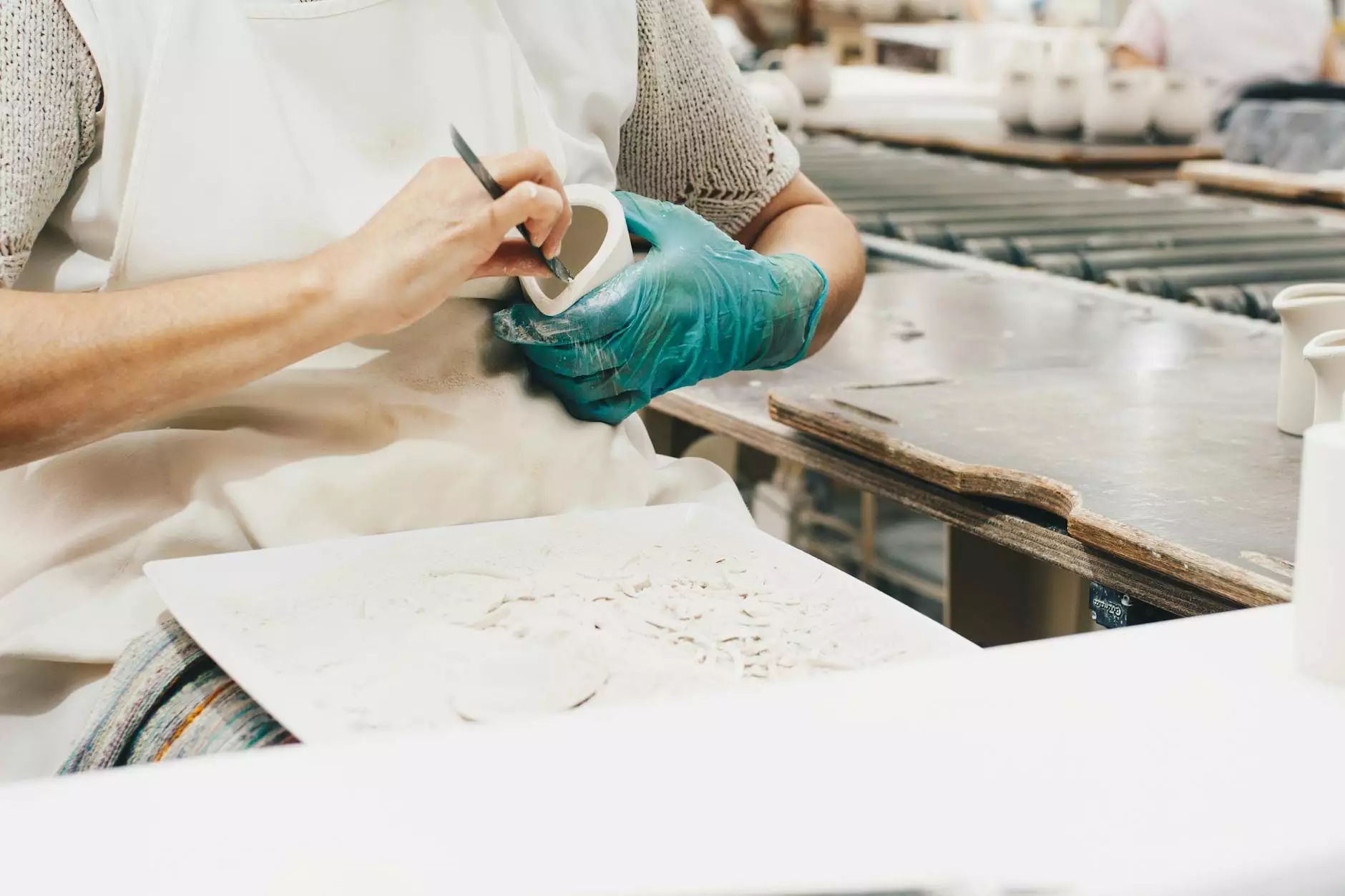
Precision plastic injection molding is a pivotal process in the manufacturing sector, playing an integral role in how products are developed and brought to market. This article will delve deep into the intricacies of this process, discussing its applications, benefits, and the reasons behind its prominence in various industries.
What is Precision Plastic Injection Molding?
At its core, precision plastic injection molding is a manufacturing technique for producing parts by injecting molten material into a mold. This versatile process allows for the creation of complex shapes and designs with exceptional accuracy, making it the go-to choice for a myriad of applications. The precision aspect refers to the ability of the process to produce components that conform to strict tolerances and specifications, essential for industries that require reliability and performance.
The Process of Precision Plastic Injection Molding
- Material Selection: The first step involves choosing the appropriate plastic material, which can vary from thermoplastics to thermosetting plastics.
- Mold Design: Engineers design a mold that reflects the desired shape of the final product, often using computer-aided design (CAD) software.
- Melting the Plastic: Chosen plastic pellets are heated until they melt and become pliable.
- Injection: The molten plastic is injected into the mold under high pressure.
- Cooling: Once filled, the mold is cooled to solidify the plastic.
- Removing the Part: After cooling, the mold opens to eject the finished part.
- Finishing Touches: Additional processes, such as trimming or surface finishing, may be conducted to achieve the final product.
Applications of Precision Plastic Injection Molding
Precision plastic injection molding finds applications across a broad spectrum of industries. Here are some primary sectors that leverage this technology:
- Automotive: From dashboard components to gear knobs and safety features, the automotive industry relies heavily on injection-molded plastics to reduce weight and improve fuel efficiency.
- Medical Devices: The medical sector requires components that are not only precise but also safe and sterilizable. Injection molding meets these needs with advanced materials and technologies.
- Consumer Electronics: The production of housings for smartphones, tablets, and other electronics heavily utilizes precision plastic injection molding for its ability to create intricate designs.
- Aerospace: Components that must withstand extreme conditions are often molded using this process, ensuring durability and reliability.
- Packaging: Custom packaging options such as bottles and containers often result from this molding technique, providing aesthetic and functional benefits.
Benefits of Precision Plastic Injection Molding
The advantages offered by precision plastic injection molding are numerous and significant. Here are some key benefits:
1. High Efficiency and Production Rates
This method allows for rapid production of large quantities of parts, significantly reducing manufacturing time and cost. The ability to create multiple parts in a single cycle is a major advantage.
2. Consistency and Precision
As the name implies, precision plastic injection molding yields consistent results, ensuring that each part produced meets stringent specifications. This is crucial for applications that rely on high precision.
3. Design Flexibility
The process allows for complex geometries that are often difficult or impossible to achieve with other manufacturing methods. This opens up a world of design possibilities for engineers and designers alike.
4. Material Versatility
A wide range of materials can be used in injection molding, from various plastics to composites, which can be selected based on the requirements of the final product.
5. Reduced Waste
With advancements in technology, precision plastic injection molding minimizes scrap and waste during production, making it a more environmentally friendly manufacturing option.
Common Challenges in Precision Plastic Injection Molding
While there are many advantages to this manufacturing process, there are also challenges that industry professionals must navigate:
1. High Initial Costs
Setting up the machinery and creating molds can require significant capital investment, which might be a barrier for small businesses.
2. Complexity of Mold Design
Designing a mold that accurately reflects the desired part can be complex and time-consuming, requiring skilled designers and engineers.
3. Process Optimization
Improper settings in the injection moulding process can lead to defects such as warping or shrinkage. Continuous monitoring and calibration of machines are essential.
4. Material Limitations
Not all plastics can be used in injection molding, and understanding material properties and the limitations is vital for successful production.
The Future of Precision Plastic Injection Molding
The precision plastic injection molding industry is on the cusp of transformation, driven by advances in technology and materials. Key trends shaping the future include:
1. Automation and Smart Manufacturing
The integration of automation in injection molding processes is enhancing efficiency and precision, allowing for lower operational costs and improved working conditions.
2. Advanced Materials
Research and development are leading to new materials that offer improved performance and flexibility in design. Biodegradable plastics are gaining traction as sustainability becomes a priority.
3. Increased Customization
As consumer preferences shift towards personalized products, the demand for customizable injection molding services is expected to rise.
4. Digital Transformation
Technology, including machine learning and IoT, is facilitating better data collection and analysis to optimize the injection molding process, resulting in higher quality and efficiency.
Conclusion
In summary, precision plastic injection molding is an essential manufacturing process that offers unparalleled benefits, from cost efficiency to design flexibility. As industries continue to evolve, so too will the methods and materials used in precision injection molding, ensuring that it remains a cornerstone of modern manufacturing. If you are considering implementing this technology in your business or looking for expert services, explore the offerings at deepmould.net for more information.
Frequently Asked Questions
1. What types of materials can be used in precision plastic injection molding?
The process can accommodate a variety of materials, including thermoplastics, thermosetting polymers, and specific composite materials tailored for unique applications.
2. How is quality control managed in precision plastic injection molding?
Quality control is typically monitored through stringent checks at various stages of the injection molding process, including material inspection, in-process testing, and final product evaluation.
3. What industries benefit the most from precision plastic injection molding?
Industries including automotive, medical, consumer electronics, and aerospace benefit significantly from this process due to their need for high-precision components.
4. How can companies optimize their injection molding processes for better performance?
Companies can optimize their processes by investing in advanced machinery, continuous training for staff, and leveraging data analytics to understand operational efficiencies.
5. Are there environmentally friendly options in precision plastic injection molding?
Yes, many manufacturers are now utilizing recyclable and biodegradable materials and focusing on reducing waste throughout the injection molding process, promoting a more sustainable approach.