Essential Guide to Pressure Vessel Testing for Safe Operations
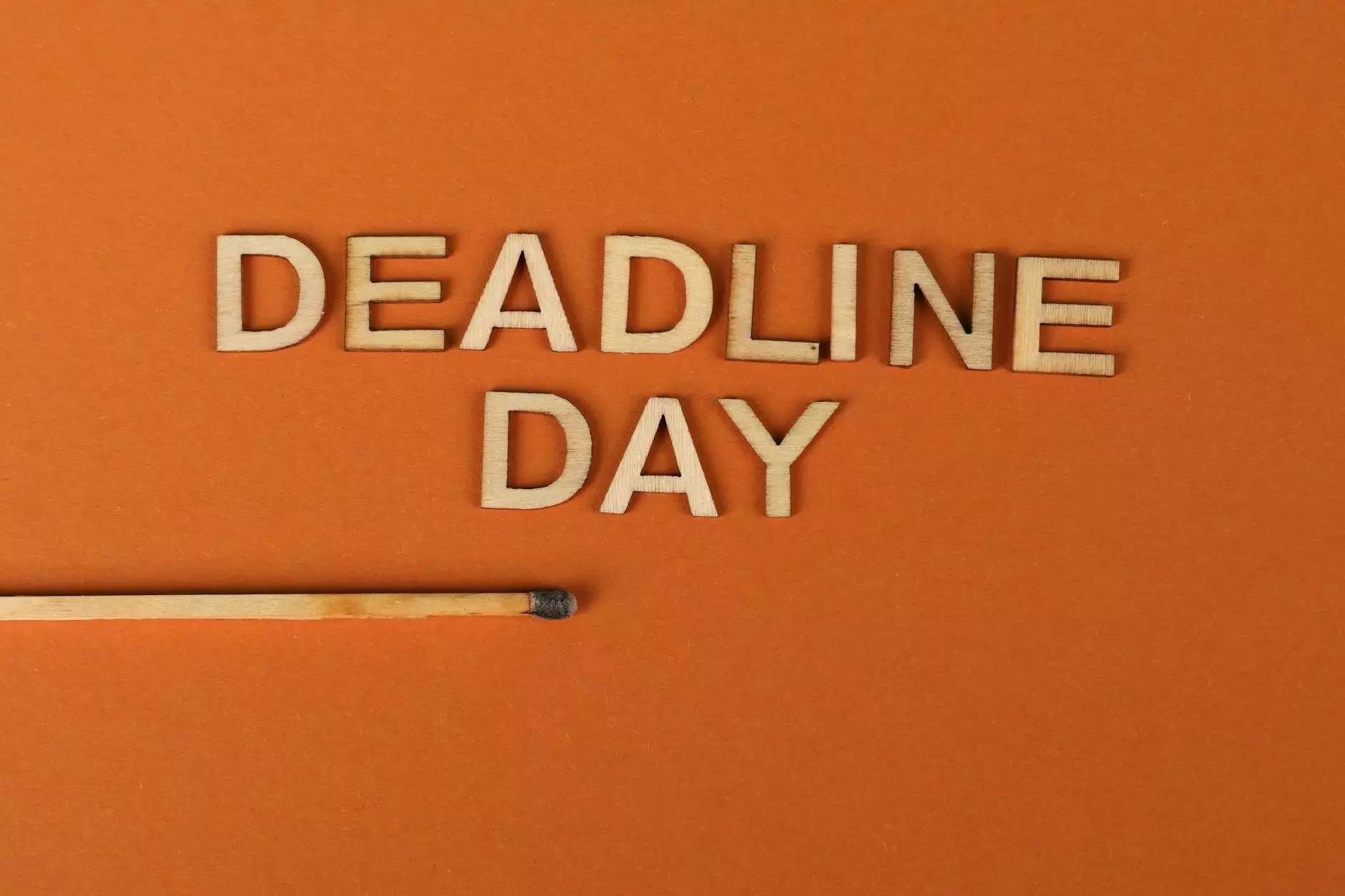
In the industrial landscape, the safety of operations hinges on the integrity of equipment, particularly pressure vessels. Pressure vessel testing is a critical aspect of this integrity, ensuring that vessels can safely contain gases or liquids under pressure. This comprehensive guide delves into the nuances of pressure vessel testing, its importance, methodologies, and how Safe Plant UK can assist in these processes.
What Are Pressure Vessels?
Pressure vessels are containers designed to hold gases or liquids at a pressure substantially different from the ambient pressure. These vessels are used extensively across various industries, including oil and gas, chemical manufacturing, and food processing. Common examples include:
- Storage tanks
- Reactors
- Boilers
- Air receivers
- Heat exchangers
The Importance of Pressure Vessel Testing
The testing of pressure vessels is paramount for several reasons:
- Safety: Regular testing mitigates the risk of explosions and leaks, protecting employees and nearby populations.
- Regulatory Compliance: Maintaining compliance with industry standards and regulations is crucial to avoid legal repercussions.
- Operational Efficiency: Testing helps ensure that vessels operate optimally, minimizing downtime and repair costs.
- Asset Longevity: Regular maintenance and testing extend the operational life of pressure vessels, providing long-term savings.
Understanding the Types of Pressure Vessel Testing
Pressure vessel testing can be categorized into several methods, each designed to assess different aspects of vessel integrity and safety.
1. Hydrostatic Testing
Hydrostatic testing involves filling the pressure vessel with water, then pressurizing it to a specified level that exceeds normal operating pressure. The vessel is monitored for leaks and deformation. This method is widely regarded for its effectiveness in detecting flaws undetectable by visual inspection.
2. Pneumatic Testing
Pneumatic testing is similar to hydrostatic testing but uses air or gas instead of water. This method poses greater risk due to the compressibility of gases but is sometimes utilized when water is impractical. Safety precautions are vital since an explosion can result from not utilizing proper care.
3. Non-Destructive Testing (NDT)
Non-destructive testing encompasses various techniques such as:
- Ultrasonic Testing: Uses high-frequency sound waves to detect internal flaws.
- Magnetic Particle Testing: Identifies surface and near-surface discontinuities in ferromagnetic materials.
- Radiographic Testing: Utilizes X-rays or gamma rays to examine internal conditions.
These methods enable inspectors to evaluate the integrity of pressure vessels without causing damage to the vessel itself.
4. Visual Inspection
Although the most basic form of testing, visual inspection remains crucial. Inspectors look for surface anomalies, signs of corrosion, or physical deformities. Regular visual inspections should always be part of a comprehensive testing program.
Standards and Regulations in Pressure Vessel Testing
Compliance with national and international standards for pressure vessels is non-negotiable. In the UK, the Pressure Systems Safety Regulations (PSSR) 2000 dictate that any pressure system should be thoroughly examined by a competent person at specified intervals.
Additionally, organizations like the American Society of Mechanical Engineers (ASME) provide guidelines through standards such as the ASME Boiler and Pressure Vessel Code (BPVC). Adhering to these regulatory guidelines helps ensure that pressure vessels are designed, constructed, and maintained safely.
Best Practices for Pressure Vessel Testing
To maintain the safety and functionality of pressure vessels, consider implementing the following best practices:
- Scheduled Inspections: Establish a rigorous schedule for inspections and testing.
- Record Keeping: Maintain detailed records of all tests, results, and actions taken for accountability and compliance.
- Training Personnel: Ensure that staff responsible for inspections have the necessary training and certifications.
- Utilizing Technology: Invest in modern technologies for continuous monitoring and advanced testing techniques.
How Safe Plant UK Can Help
At Safe Plant UK, we provide comprehensive pressure vessel testing services tailored to meet the unique needs of your operations. Our expert team guarantees that your pressure vessels comply with industry standards while promoting safety and efficiency.
Our services include:
- Thorough hydrostatic and pneumatic testing
- Advanced non-destructive testing methods
- Visual inspections and reporting
- Regulatory compliance consulting
Conclusion
In conclusion, the significance of pressure vessel testing cannot be overlooked in industrial applications. It safeguards not only the equipment but also the lives of those who operate it. Regular and meticulous testing ensures compliance with regulations, enhances operational efficiency, and extends the service life of pressure vessels.
With Safe Plant UK’s expertise, you can navigate the complexities of pressure vessel requirements with confidence, ensuring a safe and productive working environment for everyone involved. With our commitment to quality and safety, we stand ready to assist your business in achieving its operational goals through rigorous testing and compliance practices.