Unlocking the Power of Stationary Crushing Plants in Modern Electronics and 3D Printing Industries
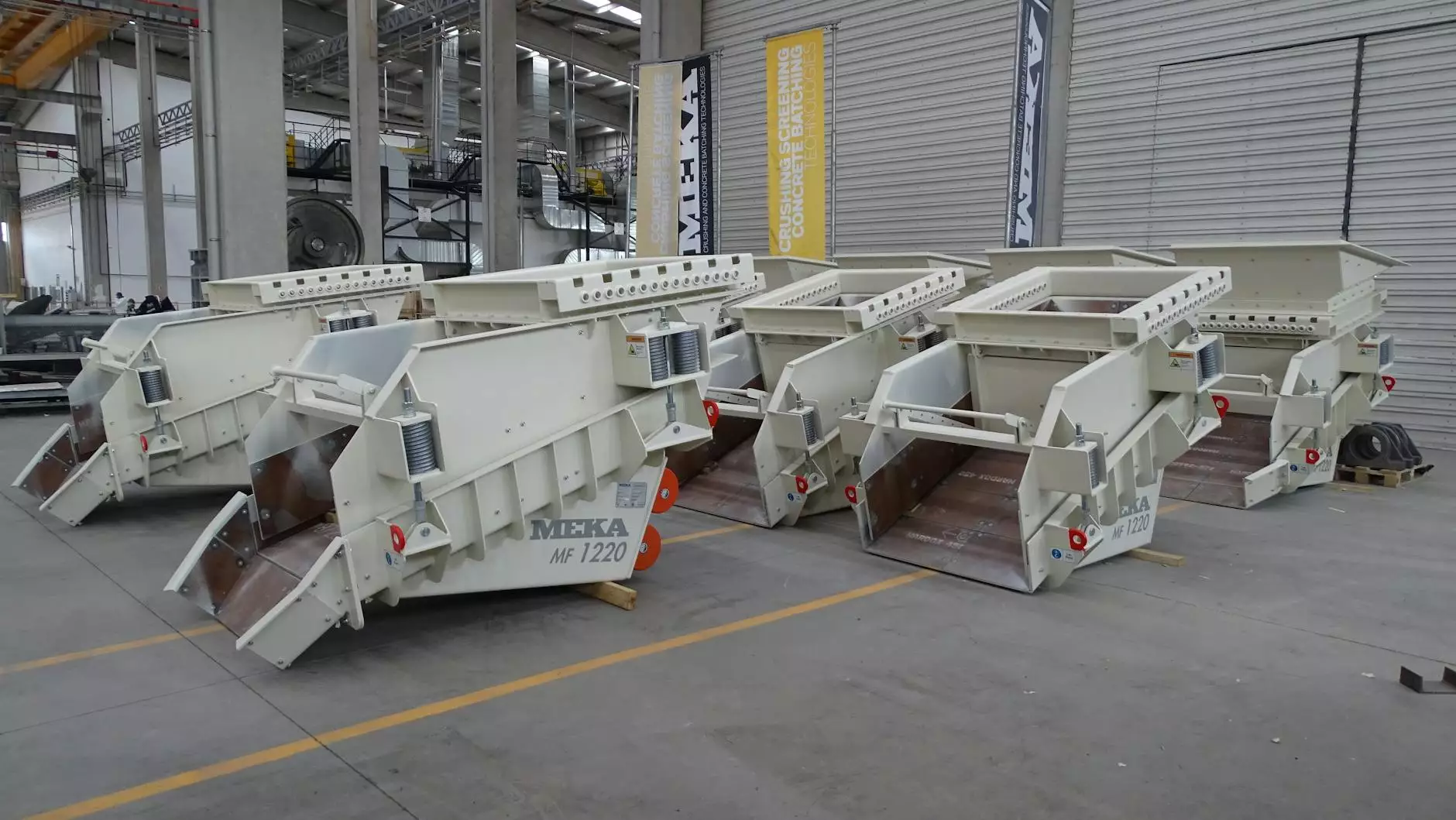
In today’s rapidly evolving technological landscape, the need for high-quality raw materials and efficient manufacturing processes is more crucial than ever. Stationary crushing plants have emerged as vital equipment, especially within the realms of electronics and 3D printing sectors, where precision, consistency, and sustainability are paramount. Companies like polygonmach.com have advanced the design and functionality of these plants, providing solutions that meet the demanding standards of modern industries. In this comprehensive guide, we will explore the significance, advantages, and applications of stationary crushing plants, emphasizing their role in electronics and 3D printing, and showcasing how they can propel your manufacturing capabilities to new heights.
Understanding Stationary Crushing Plants: Fundamentals and Features
Stationary crushing plants, also known as fixed crushing stations, are large-scale machinery setups designed to process raw materials into refined, usable forms. Unlike mobile crushers, which are built for mobility and flexibility during short-term projects, these plants are permanently installed in a designated location for continuous, high-volume production.
Key Components of a Stationary Crushing Plant
- Feeding system: Usually composed of vibrating feeders that regulate material flow and prevent blockages.
- Primary crusher: Handles initial size reduction, often using jaw crushers or gyratory crushers for coarse crushing.
- Secondary and tertiary crushers: Further refine the material through cone crushers or impact crushers, tailoring size to industry specifications.
- Conveyor belts: Seamlessly transport materials between crushing stages and towards screening units.
- Screening units: Separate materials based on size, ensuring that only appropriately processed raw materials proceed to subsequent stages.
- Control systems: Advanced automation allows for precision operation, monitoring, and maintenance scheduling.
The Role of Stationary Crushing Plants in Electronics Manufacturing
Electronics manufacturing is characterized by its requirement for high-purity raw materials, precise size reduction, and sustainable processing. Stationary crushing plants play a transformative role by enabling efficient recycling of electronic waste (e-waste) and preparation of raw mineral materials essential for semiconductor and component production.
Enhancing Material Purity and Precision
By integrating advanced crushing technology, manufacturers can achieve consistent particle sizes necessary for electronic components. The fine-tuned processing capabilities of modern stationary plants ensure that raw materials such as quartz, copper, and rare earth minerals are prepared to exact specifications, reducing impurities and enhancing product quality.
Recycling Electronic Waste Effectively
As environmental consciousness rises, e-waste recycling has become a priority. Stationary crushing plants are instrumental in dismantling and processing PCBs, circuit boards, and plastics, recovering valuable metals, and minimizing landfill waste. This not only aligns with eco-friendly practices but also reduces raw material costs.
Stationary Crushing Plants and the 3D Printing Industry
The 3D printing industry relies heavily on high-quality raw ingredients like powders, resins, and filaments. Stationary crushing plants significantly contribute to raw material preparation, especially in the creation of metal powders and fine composites used in advanced manufacturing.
Producing Metal Powders for Additive Manufacturing
High-purity metal powders are a cornerstone for metallurgical 3D printing processes such as Selective Laser Melting (SLM) or Electron Beam Melting (EBM). Stationary crushing plants equipped with milling and classification units can process raw metal chunks into ultra-fine powders with precise particle size distribution, ensuring consistency and superior print quality.
Creating Custom Material Blends for Specialized Applications
Manufacturers often need specific blends of materials—such as composite powders or alloy mixes—to develop innovative 3D printing solutions. Stationary crushing plants facilitate the systematic combination and refinement of these materials, supported by precise control systems and advanced processing technology.
Advantages of Choosing Stationary Crushing Plants from Polygonmach.com
At polygonmach.com, innovation meets reliability. Their stationary crushing plants are engineered with state-of-the-art technology, ensuring optimal performance across diverse industries, especially in electronics and 3D printing applications.
Key Benefits Include:
- High efficiency and throughput: Large-capacity equipment designed to process massive volumes of raw materials with minimal downtime.
- Enhanced durability and low maintenance: Use of premium-grade materials and engineering to extend operational life and reduce operational costs.
- Customized solutions: Equipment tailored to specific industry needs, whether processing minerals, metals, or plastics.
- Automation and smart controls: Incorporation of PLC and IoT technologies enables real-time monitoring, data collection, and optimization.
- Eco-friendly operation: Advanced dust suppression, energy-efficient motors, and recycling systems ensure sustainable processing.
Implementing a Stationary Crushing Plant: A Strategic Investment
Investing in a stationary crushing plant involves thorough planning and understanding of industry needs. Key considerations include material characteristics, projected production volume, space availability, and integration with existing manufacturing lineups.
Steps to Successful Deployment
- Assessment of raw materials: Understand the physical and chemical properties to select appropriate crushing and grinding equipment.
- Design and customization: Work with industry experts, such as those at polygonmach.com, to develop a tailored solution addressing specific processing requirements.
- Site preparation: Ensure sufficient space, appropriate foundations, and infrastructure support.
- Installation and commissioning: Expert installation, followed by rigorous testing to optimize performance.
- Staff training and maintenance planning: Empower your team with the knowledge to operate and maintain the plant efficiently.
Future Trends in Stationary Crushing Technology for Industry Advancement
The field of stationary crushing machinery continues to evolve, driven by technological innovations and industry demands for sustainability. Key trends include:
- Automation and AI integration: Building smarter plants capable of self-optimization and predictive maintenance.
- Energy-efficient technologies: Developing greener systems that reduce carbon footprint and operating costs.
- Modular systems: Increasing flexibility through easily upgradable and adaptable installation setups.
- Enhanced materials processing: Achieving finer particle sizes and better separation capabilities for specialized industry needs.
Conclusion: Elevate Your Manufacturing Capabilities with Advanced Stationary Crushing Plants
In conclusion, stationary crushing plants are indispensable for modern electronics and 3D printing industries aiming for superior material quality, operational efficiency, and environmental responsibility. By partnering with leading providers like polygonmach.com, businesses can access cutting-edge machinery tailored to their unique production requirements. Embracing this technology not only streamlines manufacturing processes but also positions companies at the forefront of innovation, sustainability, and competitiveness in the global marketplace.
Investing in a reliable, high-performance stationary crushing plant today is a strategic move towards achieving manufacturing excellence and unlocking new opportunities in the dynamic sectors of electronics and additive manufacturing.